Forum
Important Notice for New User Registrations
To combat an increasing number of spam and bot registrations, we now manually approve all new user registrations. While this may cause a delay until your account is approved, this step is essential to ensure the quality and security of this forum.
To help us verify your registration as legitimate, please use a clear name as user name or an official email address (such as a work, university, or similar address). If you’re concerned that we may not recognize your registration as non-spam, feel free to email us at with a request to approve your username.
Aeroelastic simulation for a VAWT – error during ramp-up
Quote from Adhyanth29 on 9. January 2024, 19:27Dear David,
My group is trying to perform an aeroelastic simulation of a new VAWT geometry than the Sandia 34m tutorial model. I have closely followed the tutorial approach, except that I have used the stiffness multiplier to scale up the stiffness for my model to perform a test before moving on to actual stiffness and mass properties.
However, I constantly get this error: The turbine could not be reconstructed from the structural model during ramp-up.
There is not much information on the error logs in the online documentation, so could you help me figure out what could be wrong with my setup?
I am uploading my structural files, along with the .qpr file of my simulation.
My turbine does not require cables, as it uses struts instead. So I have removed them completely.
Dear David,
My group is trying to perform an aeroelastic simulation of a new VAWT geometry than the Sandia 34m tutorial model. I have closely followed the tutorial approach, except that I have used the stiffness multiplier to scale up the stiffness for my model to perform a test before moving on to actual stiffness and mass properties.
However, I constantly get this error: The turbine could not be reconstructed from the structural model during ramp-up.
There is not much information on the error logs in the online documentation, so could you help me figure out what could be wrong with my setup?
I am uploading my structural files, along with the .qpr file of my simulation.
My turbine does not require cables, as it uses struts instead. So I have removed them completely.
Uploaded files:- You need to login to have access to uploads.
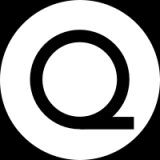
Quote from David on 11. January 2024, 13:24Hello Adhyanth,
I had a quick look at your model and with the settings that you choose it is indeed unable to solve.
Is the assumption correct that you used the structural properties of the SANDIA blade for this design, and then tried to stiffen this by applying a large stiffness multiplicator?
During aeroelastic simulations, the solver attempts to accurately represent the physical behavior of the system. If the system’s properties are unrealistic, as in your case, the solver may fail. Your application of an exceptionally high stiffness multiplier (1e4) introduces an excessive stiffness into the system. While the intention is to simulate the system as a rigid body, the solver tries to compute the actual physics, which becomes impractical with such extreme stiffnesses. A high system stiffness results in substantially increased eigenfrequencies. To accurately model this scenario, the simulation requires very fine time steps that can adequately capture these eigenfrequencies in the time domain.
One application of the stiffness tuner is indeed to be able to model a turbine behaving as a rigid body. Typically this can be achieved when increasing the original (realistic) stiffness value by a factor of ~100. In such a case, the turbine model will only exhibit very small deflections and can be treated as quasi rigid.
Regarding your model (the .qpr file), I found that adjusting the time step to 0.01s allowed the simulation to run successfully. I recommend starting with more realistic structural properties. You can then incrementally increase the stiffness, perhaps up to a factor of 100, to simulate a quasi-rigid behavior. This adjustment should also permit the use of larger time steps than the one I initially suggested.
BR,
David
Hello Adhyanth,
I had a quick look at your model and with the settings that you choose it is indeed unable to solve.
Is the assumption correct that you used the structural properties of the SANDIA blade for this design, and then tried to stiffen this by applying a large stiffness multiplicator?
During aeroelastic simulations, the solver attempts to accurately represent the physical behavior of the system. If the system’s properties are unrealistic, as in your case, the solver may fail. Your application of an exceptionally high stiffness multiplier (1e4) introduces an excessive stiffness into the system. While the intention is to simulate the system as a rigid body, the solver tries to compute the actual physics, which becomes impractical with such extreme stiffnesses. A high system stiffness results in substantially increased eigenfrequencies. To accurately model this scenario, the simulation requires very fine time steps that can adequately capture these eigenfrequencies in the time domain.
One application of the stiffness tuner is indeed to be able to model a turbine behaving as a rigid body. Typically this can be achieved when increasing the original (realistic) stiffness value by a factor of ~100. In such a case, the turbine model will only exhibit very small deflections and can be treated as quasi rigid.
Regarding your model (the .qpr file), I found that adjusting the time step to 0.01s allowed the simulation to run successfully. I recommend starting with more realistic structural properties. You can then incrementally increase the stiffness, perhaps up to a factor of 100, to simulate a quasi-rigid behavior. This adjustment should also permit the use of larger time steps than the one I initially suggested.
BR,
David
Quote from Adhyanth29 on 11. January 2024, 17:59Hi David,
Thank you for your response! Your assumption is indeed correct.
I see. Is there a study that you have conducted on the relationship between the time-step and the stiffness tuner in the past? This would be quite helpful for me to perform an aeroelastic analysis with certain components of this rotor being completely rigid.
Additionally, between yesterday and now, I played with the model a bit more (with the actual structural properties of this rotor) and I found that the model is also quite sensitive to the overdamp factor. Is this behaviour expected? I found that I had to reduce the overdamp factor by a factor of 10 to run the simulation. Although I did not think about the time-step size while playing around with this, I am mainly curious how this would affect my simulation setup.
Thanks again,
Adhyanth
Hi David,
Thank you for your response! Your assumption is indeed correct.
I see. Is there a study that you have conducted on the relationship between the time-step and the stiffness tuner in the past? This would be quite helpful for me to perform an aeroelastic analysis with certain components of this rotor being completely rigid.
Additionally, between yesterday and now, I played with the model a bit more (with the actual structural properties of this rotor) and I found that the model is also quite sensitive to the overdamp factor. Is this behaviour expected? I found that I had to reduce the overdamp factor by a factor of 10 to run the simulation. Although I did not think about the time-step size while playing around with this, I am mainly curious how this would affect my simulation setup.
Thanks again,
Adhyanth
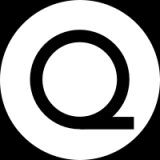
Quote from David on 11. January 2024, 22:25Hi Adhyanth,
I did not carry out such a study, but if the baseline structural properties are realistic it shouldn’t be a problem to increase the stiffness of a structural body by a factor of around 100 to model it as quasi rigid.
The overdamp factor is only implemented to reduce the large transient structural deformation during rampup through additional damping. This factor is multiplied with the damping coefficients of each structural part during the rampup phase. If you have issues solving your system with overdamping this is a strong indication that your initial damping might be unrealistically large.
The isotropic Rayleigh damping coefficient in QBlade uses only stiffness-proportional damping. Typically, structural parts such as blades or the tower have damping thats in the order of 1% critical damping. You can easily calculate the stiffness proportional damping coefficient based on the first Eigenfrequency of a structural body following the information from this ressource: https://wiki.csiamerica.com/display/kb/Damping+coefficients.
BR,
David
Hi Adhyanth,
I did not carry out such a study, but if the baseline structural properties are realistic it shouldn’t be a problem to increase the stiffness of a structural body by a factor of around 100 to model it as quasi rigid.
The overdamp factor is only implemented to reduce the large transient structural deformation during rampup through additional damping. This factor is multiplied with the damping coefficients of each structural part during the rampup phase. If you have issues solving your system with overdamping this is a strong indication that your initial damping might be unrealistically large.
The isotropic Rayleigh damping coefficient in QBlade uses only stiffness-proportional damping. Typically, structural parts such as blades or the tower have damping thats in the order of 1% critical damping. You can easily calculate the stiffness proportional damping coefficient based on the first Eigenfrequency of a structural body following the information from this ressource: https://wiki.csiamerica.com/display/kb/Damping+coefficients.
BR,
David
Quote from Adhyanth29 on 15. January 2024, 11:15Thanks for the clear explanation and the link regarding the damping coefficients, David! I had used the Sandia 34m VAWT’s Rayleigh damping coefficients for my model, which made my model have large initial damping.
Additionally, I shall take this opportunity to ask another question. In one of the later topics in the Structural Simulation forum page, you mentioned that you would demonstrate the Timoshenko beam option in QBlade for the two IEA task turbines at TORQUE 2024. Would this also be extended to VAWTs in the same release?
Best regards,
Adhyanth
Thanks for the clear explanation and the link regarding the damping coefficients, David! I had used the Sandia 34m VAWT’s Rayleigh damping coefficients for my model, which made my model have large initial damping.
Additionally, I shall take this opportunity to ask another question. In one of the later topics in the Structural Simulation forum page, you mentioned that you would demonstrate the Timoshenko beam option in QBlade for the two IEA task turbines at TORQUE 2024. Would this also be extended to VAWTs in the same release?
Best regards,
Adhyanth
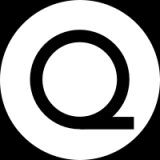
Quote from David on 15. January 2024, 12:48Hi Adhyanth,
the new Timoshenko beam element can be used for any structural part (blade, strut, tower, torquetube, substructure), regardless of turbine geometry.
BR,
David
Hi Adhyanth,
the new Timoshenko beam element can be used for any structural part (blade, strut, tower, torquetube, substructure), regardless of turbine geometry.
BR,
David
Quote from Adhyanth29 on 1. February 2024, 17:01Hi David,
After some further tests with the structural model of the VAWT (from our earlier conversations in this thread), I have been able to get the simulation of a “stiff” rotor working well. However, when I ran the realistic stiffness values, I encountered this issue: “Rotor Geometry Could Not Be Reconstructed! NaN values found in rotor Geometry.”
I am unsure where these NAN values could be encountered from the rotor geometry, as I did not encounter this during the stiff case. Could you perhaps help me out with this?
Thanks!
-Adhyanth
Hi David,
After some further tests with the structural model of the VAWT (from our earlier conversations in this thread), I have been able to get the simulation of a “stiff” rotor working well. However, when I ran the realistic stiffness values, I encountered this issue: “Rotor Geometry Could Not Be Reconstructed! NaN values found in rotor Geometry.”
I am unsure where these NAN values could be encountered from the rotor geometry, as I did not encounter this during the stiff case. Could you perhaps help me out with this?
Thanks!
-Adhyanth
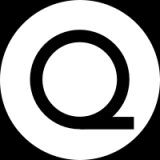
Quote from David on 2. February 2024, 07:41Hello Adhyanth,
the error message that you are getting indicates that the structural model has diverged, and thus the rotor geometry cannot be obtained after the strctural integration step.
The most likely issues for this are:
- One or more structural properties of the model are not well defined / unrealistic
- Too large accelerations during ramp-up
Things you can try:
- Set fixed rpm to zero and observe what happends during ramp-up
- Turn off initial relaxation, reduce the tmestep size, observe model ramp-up
- Increase structural iterations
I would suspect that there is an issue with the bending or torsional stiffness.
BR,
David
Hello Adhyanth,
the error message that you are getting indicates that the structural model has diverged, and thus the rotor geometry cannot be obtained after the strctural integration step.
The most likely issues for this are:
- One or more structural properties of the model are not well defined / unrealistic
- Too large accelerations during ramp-up
Things you can try:
- Set fixed rpm to zero and observe what happends during ramp-up
- Turn off initial relaxation, reduce the tmestep size, observe model ramp-up
- Increase structural iterations
I would suspect that there is an issue with the bending or torsional stiffness.
BR,
David
Quote from Adhyanth29 on 7. February 2024, 06:45Hello David,
Thanks for the suggestions. I tried all three of them that you mentioned, and I’ll list out what I observed.
- With 0 RPM, the blades showed microscopic bending in the GUI and nothing much happened.
- and 3. I tried these two options, isolated and together. But neither of them improved the simulation during ramp-up or after ramp-up. The NaN values in geometry is still the error message that I observe from this.
I used this tool called PreComp by NREL to get the spanwise distribution of the bending, edgewise, and torsional stiffness where the input is the prescribed internal structure of the blade. I suspected the stiffness values to be lower as well, so I shall try double-checking those values.
Best,
Adhyanth
Hello David,
Thanks for the suggestions. I tried all three of them that you mentioned, and I’ll list out what I observed.
- With 0 RPM, the blades showed microscopic bending in the GUI and nothing much happened.
- and 3. I tried these two options, isolated and together. But neither of them improved the simulation during ramp-up or after ramp-up. The NaN values in geometry is still the error message that I observe from this.
I used this tool called PreComp by NREL to get the spanwise distribution of the bending, edgewise, and torsional stiffness where the input is the prescribed internal structure of the blade. I suspected the stiffness values to be lower as well, so I shall try double-checking those values.
Best,
Adhyanth
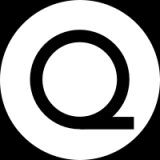
Quote from David on 7. February 2024, 09:47Hi,
I would compare the values of all structural tables in your design against an existing turbine definition in QBlade as a sanity check to see if some properties are off by orders of magnitude.
Also check the damping values, as to large damping can also cause divergence during the structural dynamics simulation.
BR,
David
Hi,
I would compare the values of all structural tables in your design against an existing turbine definition in QBlade as a sanity check to see if some properties are off by orders of magnitude.
Also check the damping values, as to large damping can also cause divergence during the structural dynamics simulation.
BR,
David
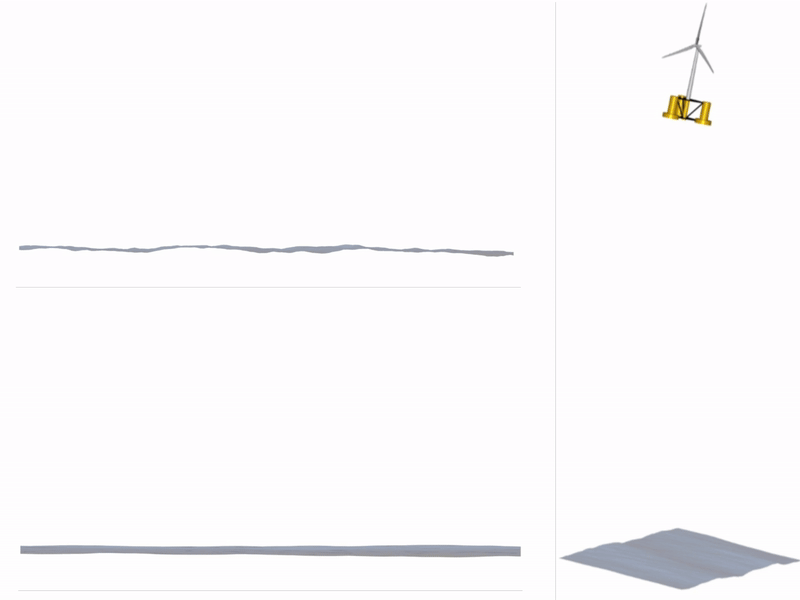