Forum
Important Notice for New User Registrations
To combat an increasing number of spam and bot registrations, we now manually approve all new user registrations. While this may cause a delay until your account is approved, this step is essential to ensure the quality and security of this forum.
To help us verify your registration as legitimate, please use a clear name as user name or an official email address (such as a work, university, or similar address). If you’re concerned that we may not recognize your registration as non-spam, feel free to email us at with a request to approve your username.
Blade definition w/o defined polars
Quote from ToddFerrante on 8. March 2023, 16:09Please allow a blade to be defined geometrically by airfoils without assigned polars.
There is an obvious workflow to use QBlade to find an optimized blade, and then export that blade geometry to CAD software for manufacture. But, CAD software doesn’t like exported geometry files with an open trailing edge. This leaves us with two paths:
A: Quickly generate standard airfoil sections, calculate polars, find the optimum blade, replace standard airfoil sections with closed airfoil sections for manufacture, export geometry to CAD.
B: Start with standard airfoil sections, create closed airfoil sections, calculate polars for closed airfoil sections, find optimum blade, export geometry to CAD.
Path A wastes time by generating a ton of polars for closed airfoil sections which are never used for anything. Path B forces the creation of closed airfoil sections which might not be used, and the calculation and use of polars for closed airfoil sections which are not numerically optimal. All of these issues would be solved if we split the workflow into two parts. The first part is doing all the theoretical work with nominal airfoil sections and polars. The second part is converting from the theoretically ideal geometry to geometry for fabrication. This is quite easy if we are able to simply replace theoretical airfoil sections with more fabrication friendly ones in the blade definition section.
In lieu of allowing use of airfoil sections without defined polars in blade definition, a way to quickly copy polars from one section to another, or even the ability to select a default placeholder polar for geometry definition would be appreciated.
Please allow a blade to be defined geometrically by airfoils without assigned polars.
There is an obvious workflow to use QBlade to find an optimized blade, and then export that blade geometry to CAD software for manufacture. But, CAD software doesn’t like exported geometry files with an open trailing edge. This leaves us with two paths:
A: Quickly generate standard airfoil sections, calculate polars, find the optimum blade, replace standard airfoil sections with closed airfoil sections for manufacture, export geometry to CAD.
B: Start with standard airfoil sections, create closed airfoil sections, calculate polars for closed airfoil sections, find optimum blade, export geometry to CAD.
Path A wastes time by generating a ton of polars for closed airfoil sections which are never used for anything. Path B forces the creation of closed airfoil sections which might not be used, and the calculation and use of polars for closed airfoil sections which are not numerically optimal. All of these issues would be solved if we split the workflow into two parts. The first part is doing all the theoretical work with nominal airfoil sections and polars. The second part is converting from the theoretically ideal geometry to geometry for fabrication. This is quite easy if we are able to simply replace theoretical airfoil sections with more fabrication friendly ones in the blade definition section.
In lieu of allowing use of airfoil sections without defined polars in blade definition, a way to quickly copy polars from one section to another, or even the ability to select a default placeholder polar for geometry definition would be appreciated.
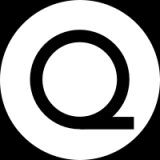
Quote from David on 9. March 2023, 18:52Hi Todd,
generally the STL file should be closed at the trailing edge. Maybe this is not working in your case since your geometry is very small and the threshold to detect whether a TE is open is too large to detect this. I have reduced this threshold so in the future it should work. Also, at the moment someone is working on the implementation of a STEP export function, and I hope to have that integrated in the near future.
Best,
David
Hi Todd,
generally the STL file should be closed at the trailing edge. Maybe this is not working in your case since your geometry is very small and the threshold to detect whether a TE is open is too large to detect this. I have reduced this threshold so in the future it should work. Also, at the moment someone is working on the implementation of a STEP export function, and I hope to have that integrated in the near future.
Best,
David
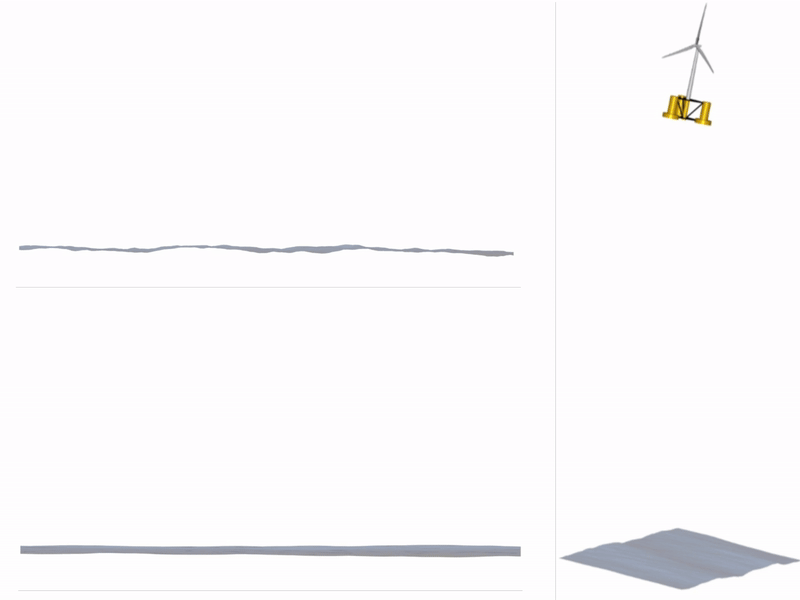