Forum
Important Notice for New User Registrations
To combat an increasing number of spam and bot registrations, we now manually approve all new user registrations. While this may cause a delay until your account is approved, this step is essential to ensure the quality and security of this forum.
To help us verify your registration as legitimate, please use a clear name as user name or an official email address (such as a work, university, or similar address). If you’re concerned that we may not recognize your registration as non-spam, feel free to email us at with a request to approve your username.
Minimum Blade Size
Quote from Zulkan on 5. June 2023, 06:21Dear Sir
I would like to inquire whether there is a minimum blade/turbine size that can be simulated in QBlade. I am currently studying QBlade and I noticed that when I conducted a simulation with a blade radius of 18 cm, I encountered errors or inconsistent data (torque, power, etc.). However, when I performed simulations with the same settings (adjusted Reynolds number, etc.) using blade radii of 2 meters, 1 meter, and 3 meters, I obtained satisfactory results. What could be the reason behind this occurrence?
Thankyou
Regards,
Zulkan
Dear Sir
I would like to inquire whether there is a minimum blade/turbine size that can be simulated in QBlade. I am currently studying QBlade and I noticed that when I conducted a simulation with a blade radius of 18 cm, I encountered errors or inconsistent data (torque, power, etc.). However, when I performed simulations with the same settings (adjusted Reynolds number, etc.) using blade radii of 2 meters, 1 meter, and 3 meters, I obtained satisfactory results. What could be the reason behind this occurrence?
Thankyou
Regards,
Zulkan
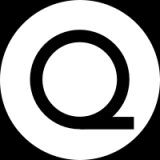
Quote from David on 5. June 2023, 11:56Hi Zulkan,
could you give an example for “inconsistent data”? In general, the simulations dont depend on the blade or totor size, but rather on the underlying aerodynamic data. That said, for very low RE numbers it is often quite difficult to obtain qualitatively good and continuous lift and drag polar data – so I guess that the polar data you are using could be the issue.
BR,
David
Hi Zulkan,
could you give an example for “inconsistent data”? In general, the simulations dont depend on the blade or totor size, but rather on the underlying aerodynamic data. That said, for very low RE numbers it is often quite difficult to obtain qualitatively good and continuous lift and drag polar data – so I guess that the polar data you are using could be the issue.
BR,
David
Quote from Zulkan on 6. June 2023, 09:43Dear Sir
Thank you for replying to my message. Here, I have attached the results of my simulation. For the blade with a radius of 18 cm, it was simulated at Reynolds numbers ranging from 5000 to 30000, while the blade with a radius of 2 meters was simulated at Reynolds numbers ranging from 70000 to 200000. In the simulation of the 2-meter blade, I have obtained a stable RPM (Revolutions Per Minute). However, for the 18 cm blade, even after 300 seconds, the RPM and other parameters are still not stable. What could be the cause?
Thankyou
Best Regards,
Zulkan
Dear Sir
Thank you for replying to my message. Here, I have attached the results of my simulation. For the blade with a radius of 18 cm, it was simulated at Reynolds numbers ranging from 5000 to 30000, while the blade with a radius of 2 meters was simulated at Reynolds numbers ranging from 70000 to 200000. In the simulation of the 2-meter blade, I have obtained a stable RPM (Revolutions Per Minute). However, for the 18 cm blade, even after 300 seconds, the RPM and other parameters are still not stable. What could be the cause?
Thankyou
Best Regards,
Zulkan
- You need to login to have access to uploads.
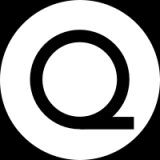
Quote from David on 6. June 2023, 15:47Hi Zulkan,
it looks like you run the first sim without limiting rpm, this means that the rotor will accelerate until it reaches the tip speed ratio at which the power coefficient is zero (so power generation is also zero). Either you need to fix the rpm or include a controller to provide some generator torque that the rotor operates at a reasonable operating point.
For the second simulation it looks like the rotor speed is increasing very slowly. This could be caused either by a very small aerodynamic torque or by a large rotational inertia.
BR,
David
Hi Zulkan,
it looks like you run the first sim without limiting rpm, this means that the rotor will accelerate until it reaches the tip speed ratio at which the power coefficient is zero (so power generation is also zero). Either you need to fix the rpm or include a controller to provide some generator torque that the rotor operates at a reasonable operating point.
For the second simulation it looks like the rotor speed is increasing very slowly. This could be caused either by a very small aerodynamic torque or by a large rotational inertia.
BR,
David
Quote from Zulkan on 12. June 2023, 07:08Dear Sir
Thank you for replying to my previous message, I did this simulation to get the rpm value if given a certain inertia without using the help of a controller (looking for rpm results by varying the inertia/material used). So in the turbine simulation settings, I use free on the rpm settings. In the 2 meter rotor simulation, I get that the rotor rpm will be stable at a certain moment. But when simulating a rotor with a radius of 18 cm, I don’t get a stable rpm even after 300 seconds. Does this happen because of a very low Reynolds number? because when I look at the cl and cl/cd graphs against AOA, I get that the high reynolds chart is more stable than the low reynolds.BR,
Zulkan
Dear Sir
Thank you for replying to my previous message, I did this simulation to get the rpm value if given a certain inertia without using the help of a controller (looking for rpm results by varying the inertia/material used). So in the turbine simulation settings, I use free on the rpm settings. In the 2 meter rotor simulation, I get that the rotor rpm will be stable at a certain moment. But when simulating a rotor with a radius of 18 cm, I don’t get a stable rpm even after 300 seconds. Does this happen because of a very low Reynolds number? because when I look at the cl and cl/cd graphs against AOA, I get that the high reynolds chart is more stable than the low reynolds.
BR,
Zulkan
- You need to login to have access to uploads.
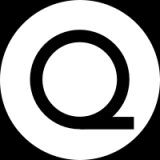
Quote from David on 12. June 2023, 11:41Hi Zulkan,
I still suspect that you somehow model the rotor inertia as being too high which means that the rotor accelerates only very slowly and the 300s are not enough for the rotor to reach the TSR at which Cp becomes zero.
Thank you for replying to my previous message, I did this simulation to get the rpm value if given a certain inertia without using the help of a controller (looking for rpm results by varying the inertia/material used).
The rpm at which the rotor stops accelerating when there is no resisting torque doesnt depend on the rotor inertia, but just on the dimensionless Cp vs TSR curve. The inertia only changes how fast the rotor can accelerate. In general, turbines will never operate at this rpm, since power output is also zero – so I would suggest either using a controller or simulating with a fixed rpm for more meaningful results.
BR,
David
Hi Zulkan,
I still suspect that you somehow model the rotor inertia as being too high which means that the rotor accelerates only very slowly and the 300s are not enough for the rotor to reach the TSR at which Cp becomes zero.
Thank you for replying to my previous message, I did this simulation to get the rpm value if given a certain inertia without using the help of a controller (looking for rpm results by varying the inertia/material used).
The rpm at which the rotor stops accelerating when there is no resisting torque doesnt depend on the rotor inertia, but just on the dimensionless Cp vs TSR curve. The inertia only changes how fast the rotor can accelerate. In general, turbines will never operate at this rpm, since power output is also zero – so I would suggest either using a controller or simulating with a fixed rpm for more meaningful results.
BR,
David
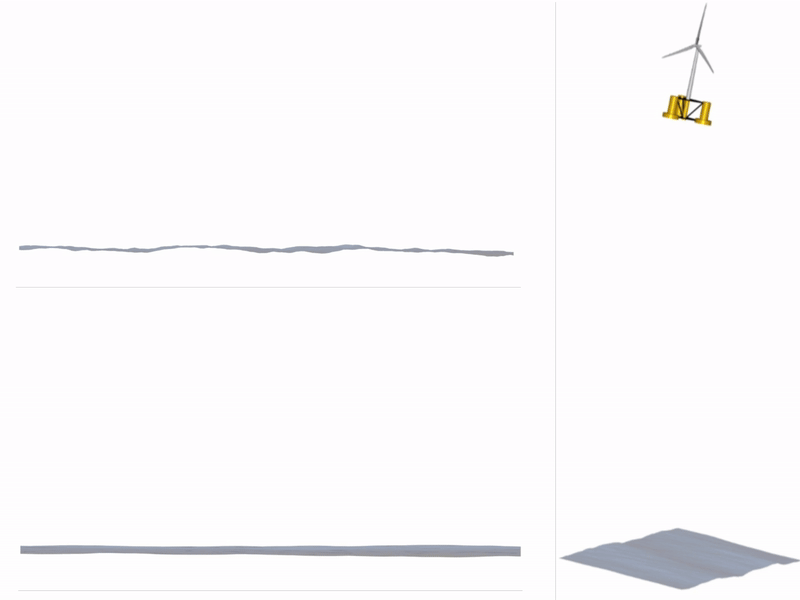