Forum
Important Notice for New User Registrations
To combat an increasing number of spam and bot registrations, we now manually approve all new user registrations. While this may cause a delay until your account is approved, this step is essential to ensure the quality and security of this forum.
To help us verify your registration as legitimate, please use a clear name as user name or an official email address (such as a work, university, or similar address). If you’re concerned that we may not recognize your registration as non-spam, feel free to email us at with a request to approve your username.
Reynolds number variation
Quote from Shayan Davani on 20. May 2024, 09:59Dear QBlade Users,
How does QBlade handle the variation of Reynolds number for different tip speed ratios? I understand that QBlade allows inputting different polars based on the specific Reynolds number and airfoil type for each blade element. However, how does it account for the variation in Reynolds number across different tip speed ratios when performing Rotor BEM?
To calculate the Reynolds number, I estimated the relative wind velocity as:
U_rel = U * sqrt(1+TSR^2)
and calculated the Reynolds number using:
Re_c = U_rel * c / 𝜈
where TSR is the tip speed ratio, U is the bulk flow velocity, “c” is the chord length, and “𝜈” is the fluid kinematic viscosity. The variation of Re along the blade and for various TSRs is shown in the attached figure.
If QBlade does not have an option to account for this variation, is it better to use a nominal TSR for calculating the Reynolds number, or would it be more accurate to take the average of Reynolds numbers over various tip speed ratios for each element?
I appreciate your help.
Best regards,
Dear QBlade Users,
How does QBlade handle the variation of Reynolds number for different tip speed ratios? I understand that QBlade allows inputting different polars based on the specific Reynolds number and airfoil type for each blade element. However, how does it account for the variation in Reynolds number across different tip speed ratios when performing Rotor BEM?
To calculate the Reynolds number, I estimated the relative wind velocity as:
U_rel = U * sqrt(1+TSR^2)
and calculated the Reynolds number using:
Re_c = U_rel * c / 𝜈
where TSR is the tip speed ratio, U is the bulk flow velocity, “c” is the chord length, and “𝜈” is the fluid kinematic viscosity. The variation of Re along the blade and for various TSRs is shown in the attached figure.
If QBlade does not have an option to account for this variation, is it better to use a nominal TSR for calculating the Reynolds number, or would it be more accurate to take the average of Reynolds numbers over various tip speed ratios for each element?
I appreciate your help.
Best regards,
Uploaded files:
- You need to login to have access to uploads.
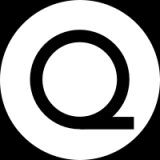
Quote from David on 21. May 2024, 17:14Hi there,
in QBlade, you can design a blade with multiple polars, spanning a range of Reynolds numbers, at each blade station.
If a blade is designed using the multi polar feature, then based on the current local Reynolds number, the polar data is interpolated.
BR,
David
Hi there,
in QBlade, you can design a blade with multiple polars, spanning a range of Reynolds numbers, at each blade station.
If a blade is designed using the multi polar feature, then based on the current local Reynolds number, the polar data is interpolated.
BR,
David
Quote from Shayan Davani on 23. May 2024, 10:03Thank you for your prompt response. It’s very interesting. I’ve been able to use multiple polars and see the difference between the results of the Single and Multi Polar options. So, if I conduct an airfoil analysis for each blade section and obtain the polars associated with different Reynolds numbers calculated based on, for example, the maximum and minimum tip speed ratios, QBlade will interpolate the polar data for any tip speed ratio between the maximum and minimum, correct? If so, the outcome will be more accurate if I use the polars for each tip speed ratio, right?
Best,
Shayan
Thank you for your prompt response. It’s very interesting. I’ve been able to use multiple polars and see the difference between the results of the Single and Multi Polar options. So, if I conduct an airfoil analysis for each blade section and obtain the polars associated with different Reynolds numbers calculated based on, for example, the maximum and minimum tip speed ratios, QBlade will interpolate the polar data for any tip speed ratio between the maximum and minimum, correct? If so, the outcome will be more accurate if I use the polars for each tip speed ratio, right?
Best,
Shayan
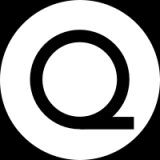
Quote from David on 27. May 2024, 17:39Hello Shayan,
you are correct. When using a multi-polar blade definition the code interpolated within the Reynolds number range specified at each blade station. In principle, this should be more accurate than using a single-polar blade definition.
BR,
David
Hello Shayan,
you are correct. When using a multi-polar blade definition the code interpolated within the Reynolds number range specified at each blade station. In principle, this should be more accurate than using a single-polar blade definition.
BR,
David
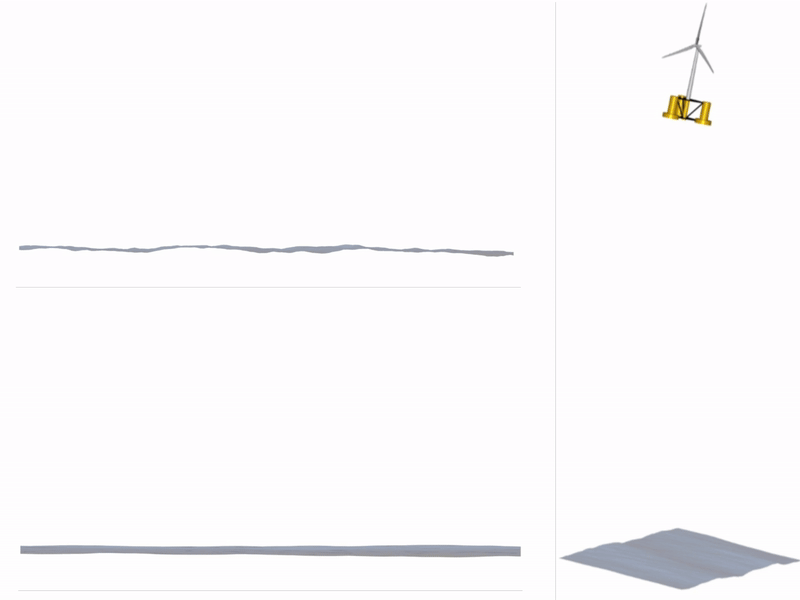