Forum
Important Notice for New User Registrations
To combat an increasing number of spam and bot registrations, we now manually approve all new user registrations. While this may cause a delay until your account is approved, this step is essential to ensure the quality and security of this forum.
To help us verify your registration as legitimate, please use a clear name as user name or an official email address (such as a work, university, or similar address). If you’re concerned that we may not recognize your registration as non-spam, feel free to email us at with a request to approve your username.
Thrust and CT for VAWT multi rotor
Quote from ThomasPotentier on 19. September 2023, 15:53Dear all,
I am simulating VAWT turbine in a multirotor (2 rotors on one support structure) configuration and I am having trouble understanding some of the outputs.
I have experimental data TSR vs CT, Qblade provides”ready to use” thrust coefficient. However, it seems odd compared to the experimental data I have. I did some more digging, I found the variable “Thrust X only” (aligned with the wind) and “Aerodynamic Thrust” from which a thrust coefficient can be calculated:
CT = 2 T / (rho * S * V^2)
Where T is either the “Thrust X only” or “Aerodynamic Thrust”, rho is the air density, S the rotor swept area (I have used both rotors) and V the wind speed at infinity. Since the wind is aligned with X, both CT are close to each other but quite far away from the “ready to use” thrust coefficient.
Moreover, I did a simulation with a single rotor and when I compare the “ready to use” thrust coefficient it is the same value as the multi rotor configuration, it is odd but can be understood since we are looking at coefficients. However, the “Aerodynamic Thrust” is almost identical between single and multi rotor configuration. Therefore, when calculating “by hand” CT the values are very different since the swept area is half the other.
I have attached a graph comparing the different tests I have performed TSR vs CT.
Qblade CT : thrust coefficient calculated by Qblade
aero thrust: thrust coefficient calculated by hand using the formula above and the “Aerodynamic Thrust” output
thrust X only: thrust coefficient calculated by hand using the formula above and the “Thrust X only” output
Thanks for any insight
Best regards,
Thomas
Dear all,
I am simulating VAWT turbine in a multirotor (2 rotors on one support structure) configuration and I am having trouble understanding some of the outputs.
I have experimental data TSR vs CT, Qblade provides”ready to use” thrust coefficient. However, it seems odd compared to the experimental data I have. I did some more digging, I found the variable “Thrust X only” (aligned with the wind) and “Aerodynamic Thrust” from which a thrust coefficient can be calculated:
CT = 2 T / (rho * S * V^2)
Where T is either the “Thrust X only” or “Aerodynamic Thrust”, rho is the air density, S the rotor swept area (I have used both rotors) and V the wind speed at infinity. Since the wind is aligned with X, both CT are close to each other but quite far away from the “ready to use” thrust coefficient.
Moreover, I did a simulation with a single rotor and when I compare the “ready to use” thrust coefficient it is the same value as the multi rotor configuration, it is odd but can be understood since we are looking at coefficients. However, the “Aerodynamic Thrust” is almost identical between single and multi rotor configuration. Therefore, when calculating “by hand” CT the values are very different since the swept area is half the other.
I have attached a graph comparing the different tests I have performed TSR vs CT.
Qblade CT : thrust coefficient calculated by Qblade
aero thrust: thrust coefficient calculated by hand using the formula above and the “Aerodynamic Thrust” output
thrust X only: thrust coefficient calculated by hand using the formula above and the “Thrust X only” output
Thanks for any insight
Best regards,
Thomas
Uploaded files:- You need to login to have access to uploads.
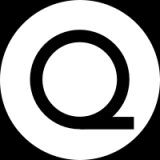
Quote from David on 20. September 2023, 18:33Hi Thomas,
the “ready to use” averaged thrust coefficient that you mention is calculated by taking the absolute value of the total rotor thrust, which combines the x, y, and z components and then normalizing it with windspeed, area, etc.
Regarding single and multi-turbine scenarios:
In a multi-turbine simulation, the aerodynamic results are individually plotted for each rotor within the configuration. For example, in a double rotor setup, two separate curves are generated. Each curve represents one of the rotors. The individual curves can be accessed from the drop-down menu shown in the attached image. The coefficients are computed using the same methodology as in the single-rotor case, based on the characteristics of each individual rotor, such as area, velocity, and so on.
When examining structural data over time, predefined variables like hub loads and tower bottom loads are also displayed for each of the individual turbines. However, it’s also possible to obtain combined loads by utilizing sensors defined in the common substructure file. These sensors are then accessible through variables stored for the “master” turbine within the multi-turbine definition. “Slave” turbines are identified by the appendix S1, S2, S3, and so forth.
BR,
David
Hi Thomas,
the “ready to use” averaged thrust coefficient that you mention is calculated by taking the absolute value of the total rotor thrust, which combines the x, y, and z components and then normalizing it with windspeed, area, etc.
Regarding single and multi-turbine scenarios:
In a multi-turbine simulation, the aerodynamic results are individually plotted for each rotor within the configuration. For example, in a double rotor setup, two separate curves are generated. Each curve represents one of the rotors. The individual curves can be accessed from the drop-down menu shown in the attached image. The coefficients are computed using the same methodology as in the single-rotor case, based on the characteristics of each individual rotor, such as area, velocity, and so on.
When examining structural data over time, predefined variables like hub loads and tower bottom loads are also displayed for each of the individual turbines. However, it’s also possible to obtain combined loads by utilizing sensors defined in the common substructure file. These sensors are then accessible through variables stored for the “master” turbine within the multi-turbine definition. “Slave” turbines are identified by the appendix S1, S2, S3, and so forth.
BR,
David
Uploaded files:- You need to login to have access to uploads.
Quote from ThomasPotentier on 26. September 2023, 09:39Dear David,
Thanks for your reply, it clarify things!
The averaged CT in a multi rotor case, is for a single rotor then ? To produce the overall CT for the entire machine I should add both the master and slave components ?
I looked at the documentation for sensor definition, I couldn’t find a way to output directly the “overall” data I need. For instance I wish to see the overall thrust generated by both rotor in the X-axis only. Is it possible to do so ?
Thanks,
Best regards,
Thomas
Dear David,
Thanks for your reply, it clarify things!
The averaged CT in a multi rotor case, is for a single rotor then ? To produce the overall CT for the entire machine I should add both the master and slave components ?
I looked at the documentation for sensor definition, I couldn’t find a way to output directly the “overall” data I need. For instance I wish to see the overall thrust generated by both rotor in the X-axis only. Is it possible to do so ?
Thanks,
Best regards,
Thomas
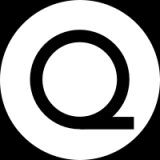
Quote from David on 26. September 2023, 10:12Hi Thomas,
you are correct – the averaged CT is computed per rotor in a multi-rotor configuration. To obtain the overall CT, it’s necessary to sum the contributions of all rotors, including both master and slave.
In the case of requesting structural loads from the common substructure of a multi-rotor turbine, the loads recorded by the sensors are however always the total loads acting on that particular part of the structure, so in your case the gravitational, aerodynamic, hydrodynamic and inertial loads generated by the entire assembly.
BR,
David
Hi Thomas,
you are correct – the averaged CT is computed per rotor in a multi-rotor configuration. To obtain the overall CT, it’s necessary to sum the contributions of all rotors, including both master and slave.
In the case of requesting structural loads from the common substructure of a multi-rotor turbine, the loads recorded by the sensors are however always the total loads acting on that particular part of the structure, so in your case the gravitational, aerodynamic, hydrodynamic and inertial loads generated by the entire assembly.
BR,
David
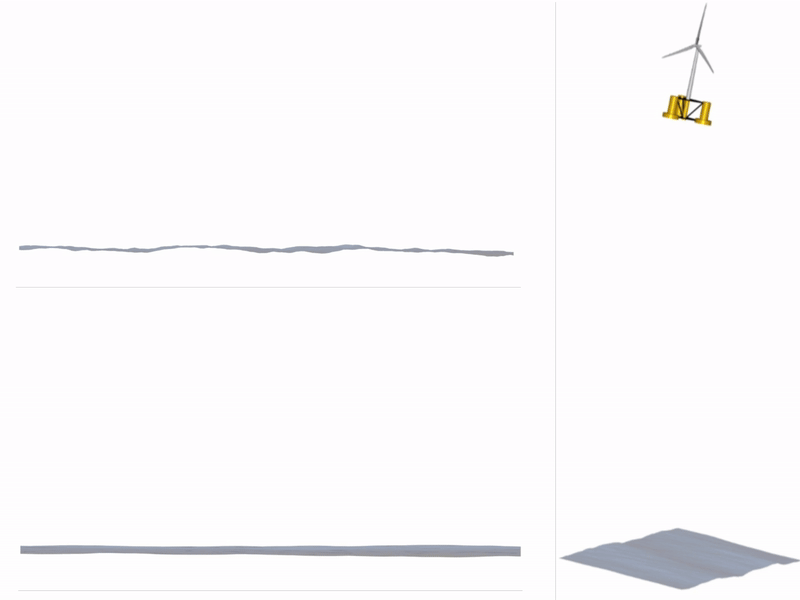