Forum
Important Notice for New User Registrations
To combat an increasing number of spam and bot registrations, we now manually approve all new user registrations. While this may cause a delay until your account is approved, this step is essential to ensure the quality and security of this forum.
To help us verify your registration as legitimate, please use a clear name as user name or an official email address (such as a work, university, or similar address). If you’re concerned that we may not recognize your registration as non-spam, feel free to email us at with a request to approve your username.
VAWT simulation timing step set up
Quote from Ron Ye on 7. February 2025, 17:26Hi,
I am using Qblade to simulate a practice VAWT project. The simulation is successful. But some detail results confused me. When I define my simulation, I need to input “Azimuthal Step” and “Number of Timesteps”. My focus is on result of Cp, Ct and Power.
I tried several “Azimuthal Step”(from 0.5-8) and “Number of Timesteps” (from 1000-80000). Every time, I got different result. I saw the Cp, Ct and Power are not convergent to a certain value. So, I set up a not-reasonable “Number of Timesteps” and let it run for over night. See the results in the attached figs.
Obviously, either Cp or Ct are not in the steady state. The difference between the Max Cp and Min Cp is about 2 times big. How do I set up the simulation parameters right to let the simulation go into steady state?
Thank you!
Ron Ye
Hi,
I am using Qblade to simulate a practice VAWT project. The simulation is successful. But some detail results confused me. When I define my simulation, I need to input “Azimuthal Step” and “Number of Timesteps”. My focus is on result of Cp, Ct and Power.
I tried several “Azimuthal Step”(from 0.5-8) and “Number of Timesteps” (from 1000-80000). Every time, I got different result. I saw the Cp, Ct and Power are not convergent to a certain value. So, I set up a not-reasonable “Number of Timesteps” and let it run for over night. See the results in the attached figs.
Obviously, either Cp or Ct are not in the steady state. The difference between the Max Cp and Min Cp is about 2 times big. How do I set up the simulation parameters right to let the simulation go into steady state?
Thank you!
Ron Ye
Uploaded files:
- You need to login to have access to uploads.
Quote from Ron Ye on 7. February 2025, 17:32Ron again,
With different wind speed and rotor speed, I realize using different “Azimuthal Step” will have different results. Is this software simulation condition dependable? What is the optimized set up to get the most accurate result?
Ron again,
With different wind speed and rotor speed, I realize using different “Azimuthal Step” will have different results. Is this software simulation condition dependable? What is the optimized set up to get the most accurate result?
Quote from FAWEI on 9. February 2025, 08:56Hi Ron,
I am also doing VAWT simulation recently. I would like to ask why the CT coefficient is greater than 1? Generally speaking, shouldn’t it be less than 0.8? The results of CT are similar to yours, and I am confused.
Regards,
Fawei
Hi Ron,
I am also doing VAWT simulation recently. I would like to ask why the CT coefficient is greater than 1? Generally speaking, shouldn’t it be less than 0.8? The results of CT are similar to yours, and I am confused.
Regards,
Fawei
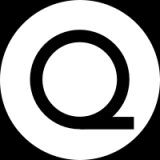
Quote from David on 10. February 2025, 11:28Hi Ron and Fawei,
simulating Vertical Axis Wind Turbines (VAWTs) can be quite challenging, as the most accurate method for capturing VAWT performance is the Lifting Line Free Vortex Wake model, which requires many parameters to be setup correctly.
Without additional details about your simulation settings, it is difficult to determine the cause of the unsteadiness in your results. Are you simulating with turbulent wind conditions? What are your Tip Speed Ratio (TSR) and turbine geometry? VAWTs inherently experience unsteady aerodynamic behavior due to continuous variations in the angle of attack during each blade rotation. Furthermore, incorrect wake settings can cause unsteadiness in the simulation results.
Regarding the parameters ”Azimuthal Step” and ”Number of Timesteps”, the Azimuthal Step is interchangeable with the Timestep Size. Given the turbine’s rotational speed, setting the Azimuthal Step automatically determines the Timestep Size, ensuring that the rotor advances by the specified Azimuthal Step per timestep. The Number of Timesteps parameter is then multiplied by the Timestep Size to determine the total simulation length. In this sense, the Simulation Length is also interchangeable with the Number of Timesteps.
Regarding the thrust coefficient (Ct), it is possible for this value to exceed 1. The exact value depends on the computed rotor thrust and the measured wind velocity. However, the definition of Ct becomes less meaningful when the turbine operates in a turbulent wind field or a boundary layer, as determining a reference wind speed, required for its calculation, becomes nontrivial in a non-uniform wind inflow setting.
BR,
David
Hi Ron and Fawei,
simulating Vertical Axis Wind Turbines (VAWTs) can be quite challenging, as the most accurate method for capturing VAWT performance is the Lifting Line Free Vortex Wake model, which requires many parameters to be setup correctly.
Without additional details about your simulation settings, it is difficult to determine the cause of the unsteadiness in your results. Are you simulating with turbulent wind conditions? What are your Tip Speed Ratio (TSR) and turbine geometry? VAWTs inherently experience unsteady aerodynamic behavior due to continuous variations in the angle of attack during each blade rotation. Furthermore, incorrect wake settings can cause unsteadiness in the simulation results.
Regarding the parameters ”Azimuthal Step” and ”Number of Timesteps”, the Azimuthal Step is interchangeable with the Timestep Size. Given the turbine’s rotational speed, setting the Azimuthal Step automatically determines the Timestep Size, ensuring that the rotor advances by the specified Azimuthal Step per timestep. The Number of Timesteps parameter is then multiplied by the Timestep Size to determine the total simulation length. In this sense, the Simulation Length is also interchangeable with the Number of Timesteps.
Regarding the thrust coefficient (Ct), it is possible for this value to exceed 1. The exact value depends on the computed rotor thrust and the measured wind velocity. However, the definition of Ct becomes less meaningful when the turbine operates in a turbulent wind field or a boundary layer, as determining a reference wind speed, required for its calculation, becomes nontrivial in a non-uniform wind inflow setting.
BR,
David
Quote from Ron Ye on 10. February 2025, 16:40Thank you very much, David:
So far, after I did some try, I found one thing that will affect the final convergence. See the following fig:
at points 1 and 3, where tip speed ratio with Cp not flat, I can repeat the same problem. However, if I move tip speed ration to 2, it convergent.
Does it indicate to me that if the turbine running at a speed close to point 1 or 3, the turbine is not stable?
Ron
Thank you very much, David:
So far, after I did some try, I found one thing that will affect the final convergence. See the following fig:
at points 1 and 3, where tip speed ratio with Cp not flat, I can repeat the same problem. However, if I move tip speed ration to 2, it convergent.
Does it indicate to me that if the turbine running at a speed close to point 1 or 3, the turbine is not stable?
Ron
Uploaded files:- You need to login to have access to uploads.
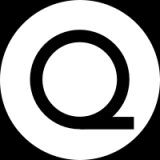
Quote from David on 10. February 2025, 17:09Hi Ron,
in general high TSR, high thrust operational points are the most challenging to simulate.
In the case of your plot this would be P3.
I would recommend to revisit your free vortex wake settings, also try deactivating the dynamic stall model or switch to the Gormont-Berg dynamic stall model.
BR,
David
Hi Ron,
in general high TSR, high thrust operational points are the most challenging to simulate.
In the case of your plot this would be P3.
I would recommend to revisit your free vortex wake settings, also try deactivating the dynamic stall model or switch to the Gormont-Berg dynamic stall model.
BR,
David
Quote from Ron Ye on 12. February 2025, 21:04Thank you very much, David,
As you mentioned, I revisited “Free Vortex” setting. I am new in this area. Would you please point me to the right parameter I need to pay attention? See the fig below.
Ron Ye
Thank you very much, David,
As you mentioned, I revisited “Free Vortex” setting. I am new in this area. Would you please point me to the right parameter I need to pay attention? See the fig below.
Ron Ye
Uploaded files:- You need to login to have access to uploads.
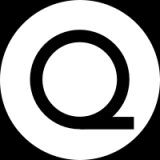
Quote from David on 13. February 2025, 08:55Dear Ron,
the optimal parameters for the free wake model depend on the rotor geometry of the turbine you are simulating.
Additionally, the timestep size should be small enough to adequately resolve a full revolution of the turbine. A good rule of thumb is to select a value corresponding to 3°–5° of azimuthal blade advancement per timestep.
In general, the default parameters should work well for most rotor designs. However, high-solidity turbine designs may require further tuning. To improve accuracy, consider adjusting the following parameters:
- Vortex core size: Try increasing the core size.
- Wake zones: Increase the sizes of the near wake and zone 1.
- Wake relaxation factor: Setting this to approximately 0.7 can help facilitate smooth wake development.
If needed, feel free to experiment with these settings until the Cp value converges continuously over time.
BR,
David
Dear Ron,
the optimal parameters for the free wake model depend on the rotor geometry of the turbine you are simulating.
Additionally, the timestep size should be small enough to adequately resolve a full revolution of the turbine. A good rule of thumb is to select a value corresponding to 3°–5° of azimuthal blade advancement per timestep.
In general, the default parameters should work well for most rotor designs. However, high-solidity turbine designs may require further tuning. To improve accuracy, consider adjusting the following parameters:
- Vortex core size: Try increasing the core size.
- Wake zones: Increase the sizes of the near wake and zone 1.
- Wake relaxation factor: Setting this to approximately 0.7 can help facilitate smooth wake development.
If needed, feel free to experiment with these settings until the Cp value converges continuously over time.
BR,
David
Quote from Ron Ye on 14. February 2025, 18:31Thank David,
I figured out the same, the best azimuthal step is about 3-5. Thank you. I feel more confident now with this setting.
I will practice more on the “Free Vortex”.
Ron
Thank David,
I figured out the same, the best azimuthal step is about 3-5. Thank you. I feel more confident now with this setting.
I will practice more on the “Free Vortex”.
Ron
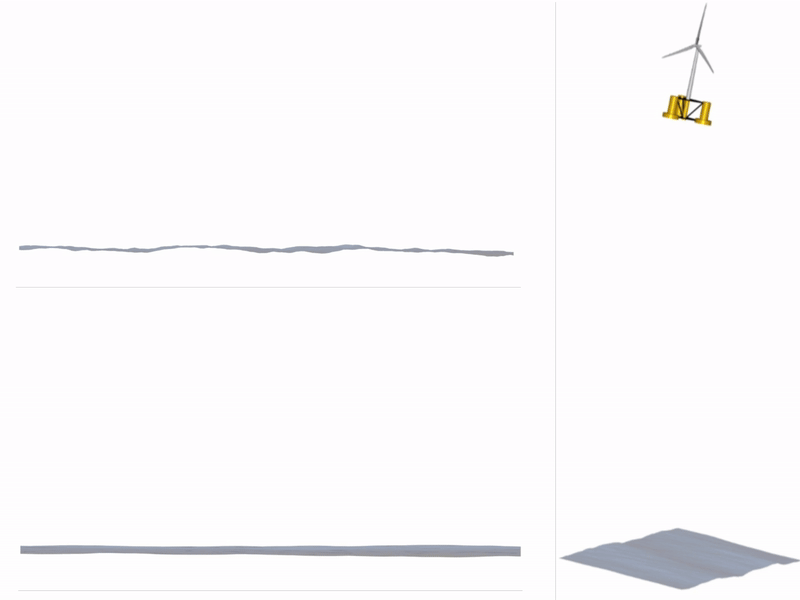